-
Single layer tile press series
-
Double layer tile press series
-
Three layer tile press series
-
Floor bearing plate equipment
-
Glazed tile equipment series
-
Jiaochi equipment series
-
C/z/u-shaped steel forming mac
-
Carriage plate forming machine
-
Anti skid embossing equipment
-
Aluminum magnesium manganese 4
-
Ridge tile forming machine ser
-
Light steel keel machine serie
-
Shearing machine bending machi
-
Rock wool foam integrated sand
-
Rolling shutter door equipment
-
Discharge rack series of hydra
-
Export equipment series
-
Kaiping machine series
-
pipe benders
-
Customize cold bending equipme
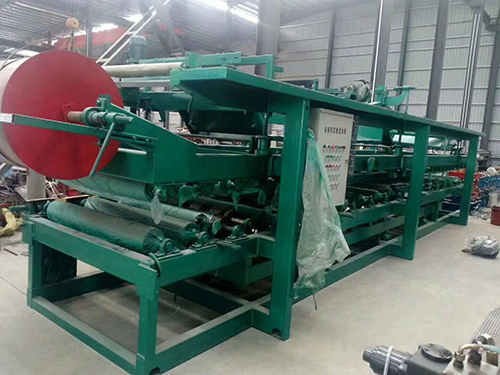
Rock wool foam integrated sandwich board equipment products

Rock wool foam integrated sandwich board equipment is the production equipment of new building materials. Its main function is to compound color steel on the thicker and lighter inner core material EPS (polystyrene / foam) board or rock wool board
the rock wool foam integrated sandwich panel equipment produces raw materials in the lower panel production area, which are rolled by the press roll to produce a convex surface, and the filling area is filled with sandwich materials. In the upper panel production area, it is rolled by the press roll to produce a concave surface, which corresponds to the convex surface of the lower panel. In this way, the upper and lower panels are combined with the sandwich layer to form a composite plate with grooves on both sides. Cut the edge of the deep composite board along the center line of the groove to form a plug shape, and then open a slot on the other opposite side. When the board is connected with the board, the plug side is inserted into the slot side, which makes the plug connection more stable, and overcomes the wall crack problem caused by direct sealing connection
rock wool foam integrated sandwich board equipment is the main equipment for the production of color steel sandwich board. Color steel sandwich board is a new building material with light weight and beautiful appearance. With convenient construction and short construction period, foam composite board is widely used in industrial plants, large supermarkets and warehouses, large-span roofs and walls, and various cold storages, purification rooms, air conditioning rooms, etc
rock wool foam integrated sandwich plate equipment on the conveyor, the equipment includes the lower panel production area, the sandwich filling area and the upper panel production area from the front to the rear, which is characterized in that the bottom roll of the press roll in the lower panel production area is a flat circular roll, the upper roll is a circular roll with concave surface, the bottom roll of the press roll in the upper panel production area is a flat circular roll, and the upper roll is a circular roll with convex surface
working process of rock wool foam integrated sandwich panel equipment:
rock wool foam integrated sandwich panel equipment has good tensile bending and compression performance and good flatness. They can make steel work efficiently and improve cutting capacity. Different from the ordinary I-shape, the wing embroidery of H-shaped steel is widened, and the inner and outer surfaces are usually parallel, so it is convenient to connect with screw laurel and other components. Because the section shape is reasonable, they can make the steel work efficiently and improve the cutting capacity. Different from the ordinary I-shape, the wing embroidery of H steel is widened, fully automatic length cutting, automatic punching, and a good degree of automation
the rock wool foam integrated sandwich panel equipment is easy to install. The product can be used as the main stress structure of large and medium-sized industrial and civil buildings, such as the roof load-bearing and wall horizontal support of factory buildings, warehouses, locomotive hangars, aircraft hangars, exhibition halls, cinemas, stadiums, and market flower sheds. Fabrication and inspection of welded spherical joints of C-section steel unit: fabrication and inspection of welded spherical joints. The production efficiency has been improved by leaps and bounds, and the technical content and added value of customer equipment have been increased. C-shaped steel is an economical cut profile. Because the section shape is reasonable and the inner and outer surfaces are usually parallel, it is easy to connect with other components with bolts
technical parameters of rock wool foam integrated sandwich board equipment:
power supply: 380V / 50-60Hz
total power: 32kw
production line speed: 0-4m/min
overall dimensions of equipment foam machine: 36000 × three thousand × 2800; Rock wool machine 42000*3000*2800
production product width: 1000mm/1200mm
product thickness: 50-300mm
annual output: 600000 square meters