-
Single layer tile press series
-
Double layer tile press series
-
Three layer tile press series
-
Floor bearing plate equipment
-
Glazed tile equipment series
-
Jiaochi equipment series
-
C/z/u-shaped steel forming mac
-
Carriage plate forming machine
-
Anti skid embossing equipment
-
Aluminum magnesium manganese 4
-
Ridge tile forming machine ser
-
Light steel keel machine serie
-
Shearing machine bending machi
-
Rock wool foam integrated sand
-
Rolling shutter door equipment
-
Discharge rack series of hydra
-
Export equipment series
-
Kaiping machine series
-
pipe benders
-
Customize cold bending equipme
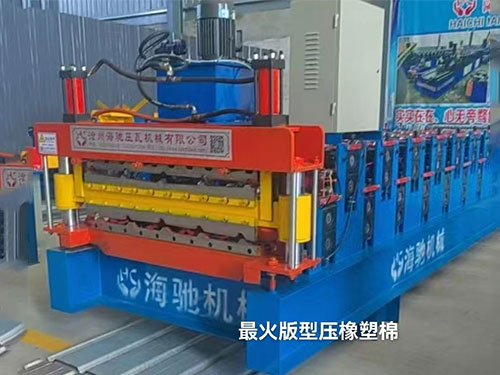
840-900 double-layer laminated rubber cotton board

840-900 double-layer laminated rubber cotton board is a mechanical equipment used for producing metal tiles. It can process metal sheets into tiles with specific shapes and sizes through rolling forming. This type of equipment usually has two layers of pressure rollers, which can simultaneously roll and shape metal sheets, improving production efficiency.
Working principle of 840-900 double-layer laminated rubber cotton board
840-900 double-layer laminated rubber cotton board is a mechanical equipment used for producing metal tiles, and its working principle mainly includes the following steps:
Power transmission: Firstly, the electric motor drives the input shaft through a pulley, which is then driven by the small and large gears to rotate the upper shaft.
Cam mechanism action: The rotation of the upper shaft drives the sliding seat equipped with the upper mold to move up and down through the cam mechanism, achieving the rolling and forming of the metal sheet.
Mold positioning: The positioning of the workbench is achieved through a gear set installed at the end of the upper shaft, which drives the pin gear and moves the groove wheel installed on the hexagonal wheel shaft to achieve indexing positioning. At both ends of the upper shaft, there is a return cam that is conjugate with the pressing cam installed on the same shaft. The accurate positioning of the lower mold in the working position is achieved through a positioning rod and a positioning plate.
Lubrication system: There are lubrication pumps installed in the left and right chassis. During machine operation, lubricating oil is transported to various friction moving parts through oil pipes to reduce wear and prolong the service life of the equipment.
Control system: The double-layer tile press adopts a thick walled three roll mirror press with suitable accuracy, which has good rigidity and can adjust the gap between the press rollers. In addition, the equipment is equipped with high-level automatic control software to achieve production information management, as well as a highly integrated networked automation control system, making the automation system perform well.
Safe measures: During use, attention should be paid to the safe operation of the equipment, such as avoiding exceeding the small closing height of the tile press, regularly adding lubricating oil, keeping the equipment clean, and taking appropriate safety measures when replacing molds or conducting mechanical debugging.