-
Single layer tile press series
-
Double layer tile press series
-
Three layer tile press series
-
Floor bearing plate equipment
-
Glazed tile equipment series
-
Jiaochi equipment series
-
C/z/u-shaped steel forming mac
-
Carriage plate forming machine
-
Anti skid embossing equipment
-
Aluminum magnesium manganese 4
-
Ridge tile forming machine ser
-
Light steel keel machine serie
-
Shearing machine bending machi
-
Rock wool foam integrated sand
-
Rolling shutter door equipment
-
Discharge rack series of hydra
-
Export equipment series
-
Kaiping machine series
-
pipe benders
-
Customize cold bending equipme
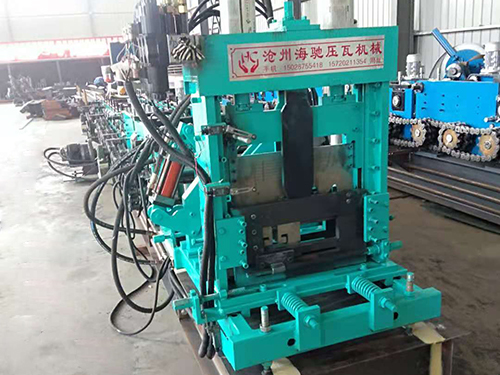
C-shaped steel cold bending equipment

C-shaped steel cold bending equipment is a set of roll forming unit that can produce various specifications of C-shaped purlin finished products. The machine is mainly composed of passive loading frame, leveling device, punching device, cutting device after forming, hydraulic station, computer control system, etc
c-steel cold bending equipment automatically cuts off and punches, which has reached the level of the same industry, and the product sales are good all over the country. Its products have beautiful appearance, reasonable structure and beautiful tile shape, which are unanimously praised by the color steel products industry
The wall thickness of section steel produced by the cold bending equipment of C section steel can be made according to the needs of span, which simplifies the production process and improves the production efficiency. It can produce various profiles with uniform wall thickness but complex cross-section shape that are difficult to produce by general hot rolling methodc-shaped steel cold bending equipment adopts automatic flying saw punching, which is easy to operate. Main uses: the product can be used as the main force bearing structure of large and medium-sized industrial and civil buildings
instructions for the use of C-shaped steel cold bending equipment:
C-shaped steel cold bending equipment is a single roll forming unit that can produce various specifications of C-shaped purlin products. The machine mainly consists of passive loading frame, leveling device, punching device, cutting device after forming, hydraulic station, computer control system, etc. This machine adopts automatic flying saw punching, which is easy to operate. The finished products of C-section steel rolled by C-section steel cold bending equipment have good tensile bending and compression performance, good flatness, fully automatic fixed length cutting, automatic punching, good degree of automation and convenient installation. The products can be used as the main stress structure of large and medium-sized industrial and civil buildings, such as the roof load-bearing and wall flat support of workshops, warehouses, locomotive hangars, aircraft hangars, exhibition halls, cinemas, stadiums, and market flower sheds. Cold formed steel is the main material for making light steel structure, which is made of steel plate or steel strip by cold bending. The wall thickness of C-beam machine can be made very thin, which simplifies the production process and improves the production efficiency. It can produce various sections with uniform wall thickness but complex cross-section shape and cold-formed sections of different materials that are difficult to produce by the general hot rolling method
c-steel cold bending equipment operation and precautions:
manual blank setting and blank taking procedures: before using the equipment, check whether the connections are stable, whether the mounting bolts and nuts are tightened, and add enough lubricating oil in the left and right chassis before powering on and starting the machine for test run. First, run the machine empty and carefully observe whether there is vibration, noise, oil coming from the oil window, and whether the movements of all components are coordinated, The mold can be installed only after the diversity is normal. When installing the mold, cut off the power supply, manually move the motor belt or big gear to rotate the workbench and raise the sliding seat to the high point, so that an object can be supported between the workbench and the bottom surface of the sliding seat to prevent the sliding seat from falling naturally, causing an accident
do not start the machine at will without knowing the structure, performance and operating procedures of the C-steel forming machine, otherwise accidents are likely to occur. It is strictly forbidden to work beyond the small closing height, that is, the small distance between the bottom surface of the upper sliding box and each working surface is 290 mm. The height of the upper and lower molds after mold closing is required to be added, and the thickness of the upper and lower base plates plus the thickness of the tile blank is not allowed to exceed 290 mm. The mold should be designed strictly according to this requirement to avoid machine tool accidents. Always observe the height of lubricating oil in the sliding box and the bodies on both sides. The equipment should be wiped frequently and kept clean. There should be no mud and water